Laser cleaning for removing contaminants from electronic components
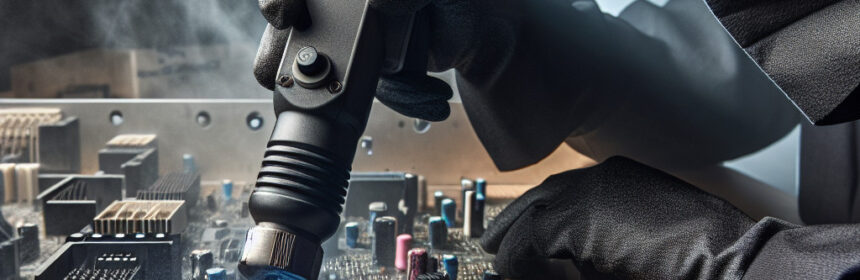
- Introduction to laser cleaning for electronic components
- Safety considerations in laser cleaning for electronic components
- Cost analysis of laser cleaning versus traditional cleaning methods
- Laser cleaning for removing dust and particles from electronic components
- Laser cleaning for removing grease and oils from electronic components
- Laser cleaning for removing thermal interface materials from electronic components
- Laser cleaning for removing contaminants from integrated circuits
- Laser cleaning for removing contaminants from memory modules
Introduction to laser cleaning for electronic components
W dzisiejszych czasach elektronika odgrywa kluczową rolę w naszym codziennym życiu. Od smartfonów po telewizory, komputery i urządzenia medyczne, elektroniczne komponenty są nieodłączną częścią naszego społeczeństwa. Jednak wraz z postępem technologicznym, pojawiają się również nowe wyzwania związane z utrzymaniem tych komponentów w czystości i sprawności. Tutaj wkracza czyszczenie laserowe, które stało się niezwykle skuteczną metodą usuwania zanieczyszczeń z elektronicznych podzespołów.
Czyszczenie laserowe jest procesem, w którym skoncentrowane wiązki laserowe są używane do usuwania zanieczyszczeń z powierzchni elektronicznych komponentów. Metoda ta jest niezwykle precyzyjna i skuteczna, ponieważ laser może być skierowany bezpośrednio na obszar, który wymaga czyszczenia, minimalizując ryzyko uszkodzenia innych części. Ponadto, czyszczenie laserowe jest nieinwazyjne, co oznacza, że nie wymaga bezpośredniego kontaktu z komponentem, co jest szczególnie ważne dla delikatnych elementów elektronicznych.
Istnieje wiele korzyści związanych z czyszczeniem laserowym dla komponentów elektronicznych. Po pierwsze, usuwanie zanieczyszczeń z powierzchni komponentów może poprawić ich wydajność i trwałość. Zanieczyszczenia, takie jak kurz, tłuszcz czy resztki lutownicze, mogą prowadzić do zakłóceń w przepływie prądu, co z kolei może prowadzić do awarii lub uszkodzenia komponentu. Czyszczenie laserowe eliminuje te zanieczyszczenia, przywracając optymalne działanie komponentów.
Po drugie, czyszczenie laserowe jest również bardziej ekologiczne niż tradycyjne metody czyszczenia. W przypadku tradycyjnych metod, takich jak czyszczenie chemiczne, często używa się substancji chemicznych, które mogą być szkodliwe dla środowiska. Czyszczenie laserowe nie wymaga stosowania żadnych substancji chemicznych, co oznacza, że jest bardziej przyjazne dla środowiska.
Ważnym aspektem czyszczenia laserowego jest również jego wszechstronność. Metoda ta może być stosowana do czyszczenia różnych rodzajów komponentów elektronicznych, takich jak płytki drukowane, układy scalone, złącza czy elementy optyczne. Bez względu na rodzaj komponentu, czyszczenie laserowe może być dostosowane do spełnienia konkretnych wymagań czyszczenia.
Warto również wspomnieć o pewnych wyzwaniach związanych z czyszczeniem laserowym dla komponentów elektronicznych. Po pierwsze, istnieje konieczność odpowiedniego doboru parametrów laserowych, takich jak moc, długość fali czy czas naświetlania. Nieprawidłowe ustawienia mogą prowadzić do uszkodzenia komponentu lub niewystarczającego czyszczenia. Dlatego ważne jest, aby proces czyszczenia był przeprowadzany przez doświadczonych specjalistów.
Podsumowując, czyszczenie laserowe jest skuteczną i precyzyjną metodą usuwania zanieczyszczeń z elektronicznych komponentów. Zapewnia ono poprawę wydajności i trwałości komponentów, jednocześnie będąc bardziej ekologicznym niż tradycyjne metody czyszczenia. Wraz z postępem technologicznym, czyszczenie laserowe staje się coraz bardziej popularne i niezastąpione w branży elektronicznej.
Słowa kluczowe: czyszczenie laserowe, komponenty elektroniczne, precyzja, wydajność, trwałość, ekologia, płytki drukowane, układy scalone, złącza, elementy optyczne.
Frazy kluczowe: czyszczenie laserowe dla komponentów elektronicznych, skuteczne usuwanie zanieczyszczeń, ekologiczne czyszczenie laserowe, precyzyjne czyszczenie elektronicznych komponentów, czyszczenie laserowe dla płytek drukowanych, czyszczenie laserowe dla układów scalonych, czyszczenie laserowe dla złącz, czyszczenie laserowe dla elementów optycznych.
Safety considerations in laser cleaning for electronic components
Another important safety consideration is the risk of fire. Laser cleaning involves the use of high-intensity beams that can generate significant heat. If the laser beam comes into contact with flammable materials, such as dust or solvents, it can ignite them and potentially cause a fire. To minimize this risk, it is essential to ensure that the cleaning area is free from any flammable substances and that appropriate fire suppression systems, such as fire extinguishers, are readily available.
Furthermore, laser cleaning can produce hazardous fumes and vapors, especially when removing certain types of contaminants, such as solder flux or adhesives. These fumes can be harmful if inhaled, leading to respiratory issues or other health problems. To mitigate this risk, it is important to conduct laser cleaning in a well-ventilated area or use local exhaust ventilation systems to remove the fumes from the cleaning zone. Additionally, operators should wear appropriate respiratory protection, such as masks or respirators, to prevent inhalation of hazardous substances.
Electrical safety is also a crucial aspect of laser cleaning for electronic components. Laser cleaning systems require a stable power supply to operate effectively. Any fluctuations or interruptions in the power supply can not only affect the cleaning process but also pose a risk of electrical shock to operators. Therefore, it is essential to ensure that the laser cleaning equipment is properly grounded and that all electrical connections are secure. Regular inspections and maintenance of the equipment should be conducted to identify and address any potential electrical hazards.
In addition to these primary safety considerations, there are several other factors that need to be taken into account when implementing laser cleaning for electronic components. These include proper training and certification of operators, adherence to safety guidelines and regulations, and regular risk assessments to identify and mitigate potential hazards.
In conclusion, laser cleaning offers significant benefits for cleaning electronic components, but it is essential to prioritize safety during the process. Eye protection, fire prevention measures, proper ventilation, electrical safety, and adherence to safety guidelines are all crucial aspects of ensuring the well-being of operators and the integrity of the electronic components being cleaned.
Keywords: laser cleaning, electronic components, safety considerations, eye protection, fire prevention, ventilation, electrical safety, risk assessment.
Long-tail phrases: laser cleaning for electronic components safety guidelines, eye protection in laser cleaning, fire prevention measures in laser cleaning, ventilation in laser cleaning, electrical safety in laser cleaning, risk assessment for laser cleaning.
Cost analysis of laser cleaning versus traditional cleaning methods
1. Chemical Cleaning:
Chemical cleaning involves the use of solvents or cleaning agents to remove contaminants from surfaces. While it is effective, it can be costly due to the purchase and disposal of chemicals. Additionally, the process may require multiple steps and longer cleaning times.
2. Abrasive Cleaning:
Abrasive cleaning utilizes abrasive materials such as sand, grit, or glass beads to physically remove contaminants. This method can be time-consuming, labor-intensive, and may result in surface damage or wear. The cost includes the purchase and disposal of abrasive materials, as well as the need for protective equipment.
3. Water Jetting:
Water jetting employs high-pressure water streams to clean surfaces. It is effective in removing loose contaminants but may not be suitable for stubborn or adhered contaminants. The cost includes water consumption, energy usage, and maintenance of water jetting equipment.
Laser Cleaning:
Laser cleaning is a non-contact, non-abrasive method that uses laser beams to remove contaminants from surfaces. It works by vaporizing or ablating the contaminants, leaving the underlying surface intact. Laser cleaning offers several advantages over traditional methods, including:
1. Precision and Selectivity:
Laser cleaning allows for precise targeting of contaminants without affecting the surrounding areas. This reduces the risk of surface damage and minimizes the need for rework or touch-ups.
2. Efficiency and Speed:
Laser cleaning is a fast process, often requiring less time compared to traditional methods. It eliminates the need for multiple cleaning steps, reducing labor costs and increasing productivity.
3. Environmental Friendliness:
Laser cleaning is a clean and environmentally friendly method as it does not involve the use of chemicals or generate hazardous waste. This reduces disposal costs and ensures compliance with environmental regulations.
Cost Analysis:
When comparing the cost of laser cleaning to traditional methods, several factors need to be considered:
1. Equipment Cost:
Laser cleaning systems can be expensive to purchase initially. However, the cost can be offset by the long-term savings in labor, consumables, and rework. Additionally, the equipment’s lifespan and maintenance requirements should be taken into account.
2. Labor Cost:
Laser cleaning requires minimal manual labor compared to traditional methods. This reduces labor costs, especially in large-scale cleaning operations. Skilled operators may be required initially, but training costs can be recovered over time.
3. Consumables and Waste Disposal:
Traditional cleaning methods often involve the use of consumables such as chemicals, abrasive materials, or water. These consumables contribute to ongoing costs and waste disposal expenses. Laser cleaning eliminates or significantly reduces the need for consumables, resulting in cost savings.
4. Rework and Touch-ups:
Traditional cleaning methods may result in surface damage or incomplete cleaning, requiring rework or touch-ups. Laser cleaning minimizes the need for rework, reducing associated costs and improving overall efficiency.
Keywords: cost analysis, laser cleaning, traditional cleaning methods, chemical cleaning, abrasive cleaning, water jetting, precision, efficiency, environmental friendliness, equipment cost, labor cost, consumables, waste disposal, rework, touch-ups.
Long-tail phrases:
1. “Cost comparison between laser cleaning and traditional cleaning methods.”
2. “Advantages of laser cleaning over chemical cleaning.”
3. “Environmental benefits of laser cleaning.”
4. “Labor cost savings with laser cleaning.”
5. “Reducing waste disposal expenses with laser cleaning.”
Laser cleaning for removing dust and particles from electronic components
One such method that has gained popularity in recent years is laser cleaning. Laser cleaning is a non-contact, non-abrasive, and precise technique that uses high-intensity laser beams to remove dust and particles from electronic components. It offers several advantages over traditional cleaning methods such as brushing, blowing, or wiping.
Firstly, laser cleaning is a highly efficient process. The laser beam can be focused on a specific area, allowing for targeted cleaning. It can remove even the tiniest particles without leaving any residue behind. This precision ensures that the electronic components are thoroughly cleaned, improving their performance and longevity.
Secondly, laser cleaning is a non-destructive method. Unlike other cleaning techniques that may involve physical contact with the components, laser cleaning does not cause any mechanical stress or damage. The laser beam gently vaporizes the contaminants, leaving the electronic parts intact. This is particularly important for delicate and sensitive components that cannot withstand harsh cleaning methods.
Moreover, laser cleaning is a safe and environmentally friendly process. It does not require the use of any chemicals or solvents, eliminating the risk of chemical residue or pollution. Additionally, laser cleaning generates minimal waste, making it a sustainable cleaning solution.
Furthermore, laser cleaning is a versatile technique that can be used for various types of electronic components. It can effectively clean printed circuit boards (PCBs), connectors, sensors, optical devices, and many other electronic parts. This versatility makes laser cleaning suitable for a wide range of industries, including electronics manufacturing, automotive, aerospace, and medical devices.
In conclusion, laser cleaning is a highly efficient, non-destructive, safe, and versatile method for removing dust and particles from electronic components. Its precision and effectiveness make it an ideal solution for maintaining the performance and reliability of electronic devices. By utilizing laser cleaning, manufacturers and users can ensure that their electronic components are free from contaminants, leading to improved product quality and customer satisfaction.
Keywords: laser cleaning, dust removal, particle contamination, electronic components, non-contact cleaning, precision cleaning, non-destructive cleaning, targeted cleaning, performance improvement, longevity, safe cleaning, environmentally friendly cleaning, versatile cleaning, printed circuit boards, connectors, sensors, optical devices, electronics manufacturing, automotive industry, aerospace industry, medical devices.
Long-tail phrases:
1. : a non-contact, non-destructive, and precise solution.
2. The advantages of laser cleaning over traditional cleaning methods for electronic components.
3. How laser cleaning improves the performance and reliability of electronic devices.
4. The safety and environmental benefits of laser cleaning for electronic components.
5. Laser cleaning: a versatile technique for various types of electronic parts.
6. The impact of laser cleaning on the electronics manufacturing industry.
7. Laser cleaning in the automotive, aerospace, and medical device sectors: a game-changer.
8. Ensuring product quality and customer satisfaction through laser cleaning of electronic components.
Laser cleaning for removing grease and oils from electronic components
One of the main advantages of laser cleaning is its precision. The laser beam can be focused to a very small spot size, allowing for precise cleaning of specific areas without affecting the surrounding components. This is particularly important in the case of electronic components, where delicate circuitry and sensitive materials are involved.
Another advantage of laser cleaning is its ability to remove contaminants without the need for any chemicals or solvents. This makes it an environmentally friendly and cost-effective cleaning method. Additionally, laser cleaning is a dry process, which means that there is no risk of introducing moisture or other liquids into the electronic components, which could potentially cause damage.
When it comes to removing grease and oils from electronic components, laser cleaning has proven to be highly effective. The high-intensity laser beam can break down the molecular bonds of the contaminants, causing them to evaporate or sublimate. This ensures that the components are thoroughly cleaned and free from any residues that could affect their performance.
Furthermore, laser cleaning can be used for both surface cleaning and precision cleaning of electronic components. Surface cleaning involves removing contaminants from the outer surface of the component, while precision cleaning involves removing contaminants from specific areas, such as solder joints or connectors. Laser cleaning can be tailored to meet the specific cleaning requirements of different electronic components, ensuring optimal results.
In addition to its effectiveness in removing grease and oils, laser cleaning offers several other benefits for electronic component cleaning. It can remove other types of contaminants, such as dust, dirt, or flux residues, without causing any damage to the components. Laser cleaning can also be used for selective cleaning, where only specific areas of the component need to be cleaned, without affecting the rest of the surface.
In conclusion, laser cleaning is a highly effective and precise method for removing grease and oils from electronic components. Its ability to remove contaminants without the need for chemicals or solvents, as well as its precision and versatility, make it an ideal choice for electronic component cleaning. By utilizing laser cleaning, manufacturers can ensure that their electronic components are thoroughly cleaned and free from any residues that could compromise their performance and reliability.
Keywords: laser cleaning, grease removal, oil removal, electronic components, precision cleaning, surface cleaning, contaminants, non-contact cleaning, non-abrasive cleaning, environmentally friendly cleaning.
Long-tail phrases: , precision cleaning of electronic components, environmentally friendly cleaning method for electronic components, non-contact and non-abrasive cleaning for electronic components, benefits of laser cleaning for electronic component cleaning.
Laser cleaning for removing thermal interface materials from electronic components
Laser cleaning is a process that utilizes high-intensity laser beams to remove contaminants or unwanted materials from surfaces. The principle behind laser cleaning lies in the interaction between the laser beam and the target material. When the laser beam is focused on the surface, it generates a high-energy density that causes the TIMs to vaporize or ablate, leaving behind a clean surface. The laser parameters such as power, pulse duration, and wavelength can be adjusted to optimize the cleaning process for different types of TIMs and electronic components.
Advantages of Laser Cleaning:
Laser cleaning offers several advantages over traditional cleaning methods when it comes to removing TIMs from electronic components. Firstly, it is a non-contact and non-abrasive process, which means that there is no physical contact between the cleaning tool and the delicate electronic components. This eliminates the risk of damage or scratching that can occur with scraping or abrasive methods. Secondly, laser cleaning is a highly precise and selective process. The laser beam can be focused on specific areas, allowing for targeted removal of TIMs without affecting the surrounding components. Additionally, laser cleaning is a dry process, eliminating the need for solvents or chemicals that can be harmful to the environment or pose health risks to operators.
Applications in the Electronics Industry:
The use of laser cleaning for removing TIMs has significant implications in the electronics industry. One of the primary applications is in the manufacturing and maintenance of electronic devices. During the manufacturing process, TIMs are often applied to ensure proper heat dissipation. However, excess TIMs or residues can lead to reduced thermal conductivity and compromised performance. Laser cleaning provides a quick and efficient solution for removing these unwanted materials, ensuring optimal heat transfer and overall device performance. In the maintenance and repair of electronic components, laser cleaning can be used to remove old or degraded TIMs, allowing for the application of new materials and extending the lifespan of the components.
Keywords: laser cleaning, thermal interface materials, electronic components, heat transfer, non-destructive, non-contact, precise, selective, manufacturing, maintenance, repair.
Long-tail phrases:
1. .
2. Non-destructive removal of thermal interface materials using laser cleaning.
3. Advantages of laser cleaning in the electronics industry.
4. Applications of laser cleaning in electronic device manufacturing.
5. Laser cleaning for extending the lifespan of electronic components.
Laser cleaning for removing contaminants from integrated circuits
One of the key advantages of laser cleaning is its ability to remove contaminants without leaving any residue or causing damage to the surface. Traditional cleaning methods, such as chemical solvents or mechanical brushing, may leave behind residues or introduce scratches, which can negatively impact the performance and reliability of ICs. Laser cleaning, on the other hand, offers a clean and residue-free surface, ensuring the optimal functioning of the integrated circuits.
Moreover, laser cleaning is a highly efficient and environmentally friendly technique. It eliminates the need for hazardous chemicals, reducing the risk of chemical exposure and pollution. The laser energy can be precisely focused on the contaminants, minimizing energy consumption and waste generation. Additionally, laser cleaning is a non-contact process, eliminating the need for physical contact with the delicate ICs, which can be prone to damage.
Laser cleaning can effectively remove various types of contaminants commonly found on ICs. Dust particles, which can accumulate during the manufacturing or packaging process, can be easily dislodged and removed by laser beams. Organic compounds, such as oils or residues from handling, can be vaporized by the laser energy, leaving a clean surface. Even stubborn contaminants, such as metal oxides or solder flux residues, can be efficiently removed through laser ablation.
In addition to its cleaning capabilities, laser technology can also be utilized for other purposes in the field of integrated circuit manufacturing. Laser marking, for example, enables the precise labeling and identification of ICs, enhancing traceability and quality control. Laser trimming allows for the fine-tuning of circuit parameters, improving the performance and yield of ICs. Laser annealing can be employed to modify the properties of materials, enhancing their electrical conductivity or optical characteristics.
In conclusion, laser cleaning has emerged as a powerful technique for removing contaminants from integrated circuits. Its non-contact nature, residue-free cleaning, and environmental friendliness make it an attractive choice for the semiconductor industry. Laser cleaning can effectively remove various types of contaminants without damaging the delicate circuitry, ensuring the reliability and functionality of ICs. Furthermore, laser technology offers additional benefits, such as marking, trimming, and annealing, contributing to the overall manufacturing process. As the demand for smaller, faster, and more reliable electronic devices continues to grow, laser cleaning is expected to play a crucial role in ensuring the quality and performance of integrated circuits.
Keywords: laser cleaning, integrated circuits, contaminants, non-contact, residue-free, selective absorption, efficiency, environmentally friendly, dust particles, organic compounds, metal oxides, solder flux residues, laser marking, laser trimming, laser annealing.
Long-tail phrases:
– : a non-contact, residue-free solution.
– The advantages of laser cleaning in the semiconductor industry.
– How laser technology enhances the manufacturing process of integrated circuits.
– The role of laser cleaning in ensuring the reliability and functionality of ICs.
– Laser cleaning: an efficient and environmentally friendly approach for IC contamination control.
Laser cleaning for removing contaminants from memory modules
One such method that has gained significant attention in recent years is laser cleaning. Laser cleaning is a non-contact, non-abrasive, and precise technique that uses high-energy laser beams to remove contaminants from surfaces. It has been widely used in various industries, including automotive, aerospace, and electronics, for cleaning delicate and sensitive components.
When it comes to memory modules, laser cleaning offers several advantages over traditional cleaning methods. Firstly, it is a non-contact method, which means there is no physical contact between the cleaning tool and the module. This eliminates the risk of damage to the delicate components and ensures a longer lifespan for the modules.
Secondly, laser cleaning is a non-abrasive method, which means it does not involve the use of any chemicals or abrasive materials that can potentially harm the modules. This is particularly important for memory modules as they are highly sensitive to external factors. The use of chemicals or abrasive materials can lead to corrosion or physical damage, compromising the performance and reliability of the modules.
Furthermore, laser cleaning is a highly precise technique that can target specific areas or contaminants on the module surface. This allows for selective cleaning, ensuring that only the contaminants are removed without affecting the surrounding components. This level of precision is crucial in maintaining the integrity and functionality of the memory modules.
In terms of efficiency, laser cleaning offers a faster and more thorough cleaning process compared to traditional methods. The high-energy laser beams can quickly and effectively remove contaminants, even from hard-to-reach areas or intricate designs. This reduces the cleaning time and increases productivity, making it an ideal solution for mass production environments.
Additionally, laser cleaning is an environmentally friendly method as it does not involve the use of chemicals or generate any hazardous waste. This aligns with the growing trend towards sustainable and eco-friendly practices in various industries.
In conclusion, laser cleaning is a highly effective and efficient method for removing contaminants from memory modules. Its non-contact, non-abrasive, and precise nature make it an ideal solution for maintaining the performance and reliability of these crucial components. With the increasing demand for memory modules and the need for higher quality and reliability, laser cleaning is poised to play a significant role in the manufacturing and maintenance processes.
Keywords: laser cleaning, contaminants, memory modules, non-contact, non-abrasive, precise, performance, reliability, selective cleaning, efficiency, environmentally friendly.
Long-tail phrases:
1. Laser cleaning for memory module contamination removal.
2. Advantages of laser cleaning in memory module maintenance.
3. Non-contact and non-abrasive cleaning for memory modules.
4. Precision cleaning for memory module contaminants.
5. Efficient and eco-friendly cleaning method for memory modules.
- Laser cleaning for removing contaminants from electronic components - 25 January 2024