Laser cleaning for removing contaminants from aerospace components
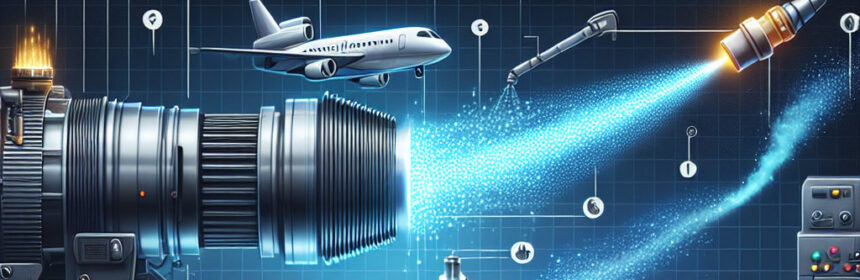
- Benefits of Laser Cleaning in Aerospace Industry
- Laser Cleaning Technology for Aerospace Components
- Importance of Contaminant Removal in Aerospace Components
- Laser Cleaning Process for Aerospace Applications
- Advantages of Laser Cleaning for Aerospace Maintenance
Benefits of Laser Cleaning in Aerospace Industry
Improved Efficiency
One of the key benefits of laser cleaning in the aerospace industry is improved efficiency. Traditional cleaning methods often require time-consuming manual labor and the use of chemicals that can be harmful to both workers and the environment. Laser cleaning, on the other hand, is a fast and efficient process that can be automated to clean large areas quickly and effectively.
Cost Savings
Another major benefit of laser cleaning is cost savings. While the initial investment in laser cleaning equipment may be higher than traditional cleaning methods, the long-term savings are significant. Laser cleaning eliminates the need for expensive chemicals and abrasive materials, as well as the labor costs associated with manual cleaning. Additionally, laser cleaning is a non-contact process that reduces wear and tear on equipment, leading to lower maintenance costs over time.
Environmental Benefits
Laser cleaning is also environmentally friendly. Traditional cleaning methods often involve the use of harsh chemicals that can be harmful to the environment and pose health risks to workers. Laser cleaning, on the other hand, is a clean and sustainable process that does not produce any hazardous waste or emissions. This makes it an ideal choice for aerospace companies looking to reduce their environmental impact and comply with strict regulations.
Improved Quality
One of the most important benefits of laser cleaning in the aerospace industry is improved quality. Laser cleaning is a precise and controlled process that can remove contaminants and coatings without damaging the underlying surface. This ensures that critical aerospace components remain in optimal condition, leading to improved performance and reliability. Additionally, laser cleaning can be used to achieve a higher level of cleanliness than traditional methods, reducing the risk of contamination and defects in aerospace products.
Applications of Laser Cleaning in Aerospace Industry
Laser cleaning has a wide range of applications in the aerospace industry, including:
Application | Description |
---|---|
Surface Preparation | Laser cleaning is used to prepare surfaces for bonding, welding, and painting by removing contaminants and oxides. |
Component Maintenance | Laser cleaning is used to remove coatings, corrosion, and other contaminants from critical aerospace components. |
Tool Cleaning | Laser cleaning is used to clean molds, dies, and other tooling used in aerospace manufacturing. |
Conclusion
Laser cleaning is a game-changing technology that offers a wide range of benefits to the aerospace industry. From improved efficiency and cost savings to environmental benefits and improved quality, laser cleaning is revolutionizing the way aerospace companies clean and maintain critical components. As the aerospace industry continues to evolve, laser cleaning will play an increasingly important role in ensuring the safety, reliability, and performance of aerospace products.
Laser Cleaning Technology for Aerospace Components
How Laser Cleaning Works
Laser cleaning works by using a high-powered laser beam to remove contaminants from the surface of a material. The laser beam is focused on the surface of the component, where it vaporizes the contaminants without damaging the underlying material. This process is highly precise and can be controlled to remove only the contaminants, leaving the surface of the component clean and undamaged.
Benefits of Laser Cleaning Technology
There are several benefits to using laser cleaning technology for aerospace components:
Benefit | Description |
---|---|
Efficiency | Laser cleaning is a fast and efficient process, reducing cleaning time and labor costs. |
Precision | Laser cleaning is highly precise, allowing for targeted removal of contaminants without damaging the component. |
Environmentally Friendly | Laser cleaning does not require the use of chemicals or abrasive materials, making it an environmentally friendly cleaning option. |
Cost-Effective | While the initial investment in laser cleaning technology may be higher than traditional cleaning methods, the long-term cost savings make it a cost-effective option. |
Applications of Laser Cleaning in Aerospace
Laser cleaning technology is used in a variety of aerospace applications, including:
Application | Description |
---|---|
Engine Components | Laser cleaning is used to remove carbon deposits and other contaminants from engine components, improving performance and efficiency. |
Aircraft Surfaces | Laser cleaning is used to remove paint, corrosion, and other contaminants from aircraft surfaces, improving aerodynamics and reducing maintenance costs. |
Electronic Components | Laser cleaning is used to remove solder flux and other contaminants from electronic components, improving reliability and performance. |
Conclusion
Laser cleaning technology offers a more efficient, precise, and environmentally friendly alternative for cleaning aerospace components. With its many benefits and applications, laser cleaning is becoming an increasingly popular choice for aerospace maintenance and cleaning tasks.
Importance of Contaminant Removal in Aerospace Components
1. Safety
Contaminants such as dirt, dust, and debris can compromise the structural integrity of aerospace components, leading to potential safety hazards. Removing these contaminants is essential to prevent accidents and ensure the safety of passengers and crew members.
2. Performance
Contaminants can also affect the performance of aerospace components by causing friction, corrosion, or other issues that can lead to malfunctions. By removing contaminants, aerospace components can operate more efficiently and effectively, improving overall performance.
3. Durability
Contaminants can accelerate wear and tear on aerospace components, reducing their lifespan and increasing the need for maintenance and repairs. By removing contaminants, aerospace components can last longer and require less frequent maintenance, saving time and money in the long run.
4. Regulatory Compliance
The aerospace industry is highly regulated, with strict standards and requirements for the cleanliness of components. Failure to remove contaminants can result in non-compliance with these regulations, leading to fines, penalties, and potential legal issues. It is essential to remove contaminants to ensure compliance with industry standards.
5. Reliability
Contaminants can cause aerospace components to fail unexpectedly, leading to costly repairs, delays, and disruptions in operations. By removing contaminants, aerospace components can operate more reliably and consistently, reducing the risk of unexpected failures and ensuring smooth operations.
6. Quality Assurance
Contaminant removal is an essential part of quality assurance in the aerospace industry. By ensuring that components are free from contaminants, manufacturers can guarantee the quality and reliability of their products, building trust with customers and maintaining a strong reputation in the industry.
7. Environmental Impact
Contaminants in aerospace components can also have a negative impact on the environment, especially if they are released into the air or water during operation. By removing contaminants, aerospace manufacturers can reduce their environmental footprint and contribute to a cleaner and healthier planet.
8. Cost Savings
By removing contaminants from aerospace components, manufacturers can avoid costly repairs, replacements, and downtime caused by malfunctions or failures. Investing in contaminant removal can lead to significant cost savings in the long term, making it a wise investment for aerospace companies.
Conclusion
Contaminant removal is a critical process in the aerospace industry, with implications for safety, performance, durability, regulatory compliance, reliability, quality assurance, environmental impact, and cost savings. By prioritizing contaminant removal in aerospace components, manufacturers can ensure that their products meet the highest standards and deliver optimal performance, safety, and reliability.
Laser Cleaning Process for Aerospace Applications
How Does Laser Cleaning Work?
Laser cleaning works by using a high-intensity laser beam to vaporize contaminants on a surface. The laser beam is focused on the surface, and the energy from the beam causes the contaminants to evaporate, leaving behind a clean surface. The process is non-abrasive and does not damage the underlying material, making it ideal for delicate aerospace components.
Benefits of Laser Cleaning
- Non-contact: Laser cleaning does not require physical contact with the surface, reducing the risk of damage to delicate components.
- Environmentally friendly: Laser cleaning does not use chemicals or produce waste, making it a clean and sustainable method of cleaning.
- High precision: Laser cleaning can be controlled with high precision, allowing for targeted cleaning of specific areas.
- Efficient: Laser cleaning is a fast and efficient process, reducing downtime and increasing productivity.
Applications in the Aerospace Industry
Laser cleaning is used in a variety of applications in the aerospace industry, including:
- Surface preparation: Laser cleaning is used to prepare surfaces for bonding, painting, or coating by removing contaminants and oxides.
- Component maintenance: Laser cleaning is used to remove corrosion, paint, and other contaminants from aerospace components to extend their lifespan.
- Tool cleaning: Laser cleaning is used to clean molds, dies, and other tooling used in aerospace manufacturing processes.
Conclusion
Laser cleaning is a versatile and efficient method of cleaning aerospace components. Its non-contact nature, environmental friendliness, and high precision make it an ideal choice for the aerospace industry. By using laser cleaning, aerospace manufacturers can ensure the cleanliness and safety of their components while increasing productivity and efficiency.
Advantages of Laser Cleaning for Aerospace Maintenance
Efficiency
Laser cleaning is a highly efficient method of removing contaminants from aerospace components. The focused laser beam can quickly and effectively remove dirt, grease, paint, and other residues without damaging the underlying material. This results in faster cleaning times and reduced downtime for maintenance tasks.
Precision
One of the major advantages of laser cleaning is its precision. The laser beam can be precisely controlled to target specific areas on a component, allowing for selective cleaning without affecting surrounding surfaces. This level of precision is crucial in aerospace maintenance, where even minor damage to a component can have serious consequences.
Safety
Laser cleaning is a safe and environmentally friendly method of cleaning aerospace components. Unlike traditional cleaning methods that use harsh chemicals or abrasive materials, laser cleaning does not produce any harmful fumes or waste. This makes it a safer option for both workers and the environment.
Cost-Effectiveness
While the initial investment in laser cleaning equipment may be higher than traditional cleaning methods, the long-term cost savings can be significant. Laser cleaning is a more efficient and precise method of cleaning, which can result in reduced maintenance costs and extended equipment lifespan. Additionally, the reduced need for cleaning chemicals and abrasive materials can lead to further cost savings.
Versatility
Laser cleaning is a versatile method that can be used on a wide range of aerospace components, including engine parts, landing gear, and fuselage panels. It can be used to remove a variety of contaminants, such as rust, corrosion, and paint, making it a valuable tool for aerospace maintenance tasks.
Non-Destructive
Unlike some traditional cleaning methods that can damage or weaken aerospace components, laser cleaning is a non-destructive method that preserves the integrity of the material. This is particularly important in the aerospace industry, where the structural integrity of components is critical for safety and performance.
Conclusion
Overall, laser cleaning offers numerous advantages for aerospace maintenance tasks. Its efficiency, precision, safety, cost-effectiveness, versatility, and non-destructive nature make it an ideal choice for cleaning aerospace components. As technology continues to advance, laser cleaning is likely to become an increasingly important tool in the aerospace industry.
- Laser cleaning for removing contaminants from aerospace components - 31 July 2024
- Laser cleaning for removing adhesive residues - 19 April 2024
- CSR at WebMakers - 19 April 2024